A partner for affordable, sustainable mobility
Vehicle manufacturers and suppliers recognize their responsibility to act on climate change, reduce emissions across their entire value chain, and develop circularity in their sourcing models.
Wheels are a priority for action. Their production is energy-intensive, and the raw materials pose challenges. Significantly increasing the share of sustainable and recycled materials in wheels by 2030 is a key ambition for Maxion Wheels.
The transition towards a circular economy requires Maxion Wheels to minimize the use of primary raw materials, eliminate waste, and keep suitable automotive-grade wheel materials in circulation for wheel applications for longer.
In 2023, with the goal to reduce CO2 equivalent emissions to the lowest possible level for two existing series production light vehicle wheels, Maxion Wheels launched two ultra-low CO2 wheel pilot programs – one for steel – one for aluminum.
A global cross-functional team with representatives from Engineering, Supply Chain, Operations, Sustainability and Marketing kicked off the work in February and finished in August with the pilot wheels demonstrating the viability of the “green” materials and processes. The verified results were communicated from the automotive industry’s mega event, IAA Mobility in Germany.
The following highlights the team’s work.
First of a new generation of secondary aluminum wheels
Maxion Wheels’ commitment to developing truly sustainable and affordable wheel options has produced a new generation of alloy wheels. Made using 100 percent secondary aluminum, sourced exclusively from recycled post-consumer alloy wheels, the 15” wheel demonstrates the scale of CO2 reductions possible in series production – and the benefits of circular business collaborations.
Manufactured at Maxion Wheels light vehicle aluminum wheels plant in Santo André, Brazil, the pilot uses the company’s recycling partners and own energy-efficient melting process. Cradle-to-gate CO2 emissions for the finished wheels are 62 percent lower than for the same current alloy wheel produced using primary aluminum.
Maxion Wheels is developing partnerships to increase the number of wheels it can produce with secondary aluminum. Collaborations with customers are a critical step in realizing the full potential of circular sourcing models.
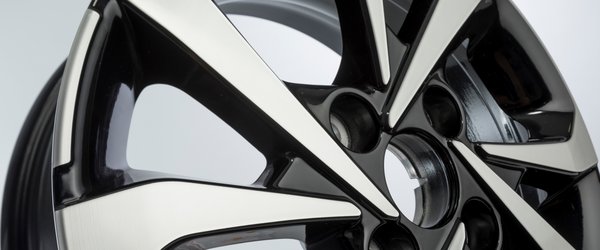
CIRCULAR CAPABILITIES PROVEN
The Brazil project followed an existing customer wheel design with the automaker defining the styling and specifications. The secondary aluminum was produced by recycling post-consumer alloy wheels. Maxion Wheels works with supply chain partners to source the wheels and separate them from other materials and contaminants.
The wheels are shot blasted, completely removing residual paint. Once clean, the aluminum wheels are melted, and the chemical composition adjusted to ensure the alloy meets OEM specifications.
SCALING UP CO2 SAVINGS
Maxion Wheels has mapped CO2 equivalent emissions for the recycled material process to the same standards as for its series production programs. Produced in Brazil using hydroelectric power, CO2 emissions for the finished wheels are less than 2.14kg CO2 per kilogram of wheel.
An identical wheel made in the same plant using primary aluminum would have a CO2 footprint of 5.60kg CO2 per kilogram of finished product.
The energy mix in Brazil makes our aluminum wheel facilities in Santo André and Limeira ideal sourcing locations for sustainable wheels. Although different locations naturally have different Scope 1 and 2 profiles, the benefit of substituting primary aluminum with secondary material is universal.
Scaling up this project will be possible with further development of supplier capacity. The main barrier to mass production is cost and availability.
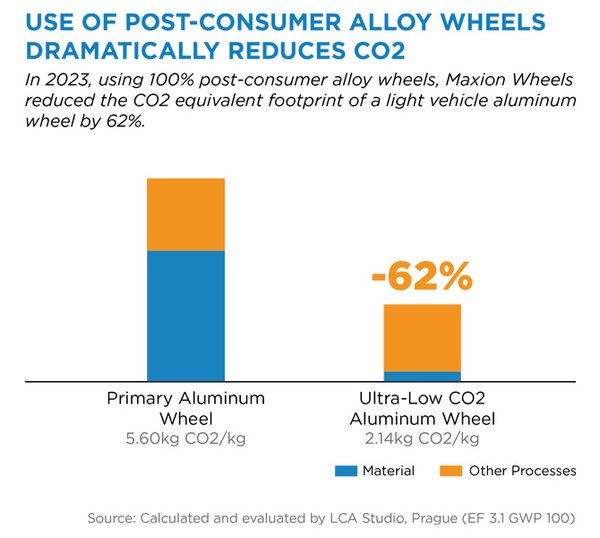
“Confidence in the performance and finish quality is no longer a question. The development of a new secondary material supply base is running fast, and strategies for greener raw materials purchasing are starting to solidify.”
Materials key to carbon neutral wheels
Renewable energy can reduce the CO2 equivalent footprint of a wheel, but the biggest opportunity lies in the emissions-intensive raw materials wheels use. Around 75-85 percent of a wheel’s CO2 footprint is from the raw material, regardless of whether it’s steel or aluminum.
Conventional primary aluminum is the most CO2 equivalent intensive. For each kilogram of primary aluminum produced, depending on the energy source, 3.5 to 25 kg of CO2 is released into the atmosphere. Production of a kilogram of conventional primary steel emits 2 to 2.5kg of CO2. With conventional steel’s significant advantage over aluminum, switching to steel can provide immediate reductions. Long-term alternatives are needed, however, for mobility to become carbon neutral.
To read more about Maxion Wheels' sustainability product transformation projects, read our white paper, Maxion Wheels Sustainable Wheel Strategies for CO2 Savings.